分享:航空復合材料-金屬連接結構的拉伸性能及其漸進損傷
張浩宇1,侯 波2,何宇廷3,馮 宇3,譚翔飛3
(1.中國人民解放軍95906部隊,北京 102206;
2.陸軍航空兵研究所,北京 101121;3.空軍工程大學工程學院,西安 710038)
摘 要:利用有限元軟件建立了某型飛機復合材料G金屬連接結構件模型,以改進的 Camanho損傷退化模型作為失效判定準則,模擬了該連接結構件的拉伸性能和損傷累積過程并進行了試驗驗證.結果表明:在加裝防彎夾具后,復合材料G金屬連接結構件的拉伸試驗結果更加準確,拉伸破壞模式由拉脫破壞變?yōu)閿D壓破壞;在較小的拉伸載荷下,其應變隨載荷的增加呈線性增大,在金屬上的應變明顯大于復合材料層合板上的;損傷從復合材料和金屬連接螺栓處產生,隨載荷的增大逐漸累積并沿螺栓擠壓方向擴展;模擬得到的最終破壞載荷為90kN,與試驗值的相對誤差僅為6.5%,證明了模擬結果的準確性.
關鍵詞:復合材料;累積損傷;連接結構;失效準則;抗拉強度
中圖分類號:V257 文獻標志碼:A 文章編號:1000G3738(2017)08G0087G06
TensilePropertyofAeronauticalCompositeGMetalJointStructureandItsProgressiveDamage
ZHANGHaoyu1,HOUBo2,HEYuting
3,FENGYu3,TANXiangfei3
(1.No.95906TroopsofPLA,Beijing102206,China;2.ArmyAviationResearchInstitute,Beijing101121,China;3.EngineeringCollege,AirForceEngineeringUniversity,Xi′an710038,China)
Abstract:ThemodelofthecompositeGmetaljointstructureofonetypeaircrafewasestablishedusingthe
finiteelementsoftware.Then withthe modifiedCamanhodamagedegradation modelasthecriterionoffailure
judgment,thetensilepropertyanddamageaccumulationprocessofthejointstructureweresimulatedandverified
bythetests.TheresultsshowthatafterassembledwiththeantiGbendingfixture,thetensiletestresultsofthe
compositeGmetaljointstructureweremoreaccurateandthetensiledamagemodechangedfrom pullGofffailuretocrushingfailure.Underrelativelylowtensileloads,thestrainincreasedlinearlywiththeincreaseofloadandwas
obviouslylargeronthemetalthanonthecompositelaminate.Thedamagewasproducedfromtheconnectingbolts
betweenthecompositeandmetal,thenaccumulatedgraduallyandextendedalongthecompressivedirectionoftheboltswiththeincreaseofload.Thesimulatedfinaldestructionloadwas90kNwiththerelativeerrorofonly6.5%comparingtothetestresult,indicatingtheaccuracyofthesimulation.
Keywords:composite;accumulateddamage;jointstructure;failurecriterion;tensilestrength
0 引 言
復合材料因具有比強度和比模量高、性能可設計和易于整體成形等優(yōu)點而在航空、航天結構上得到了廣泛應用.但是,當前服役飛機結構中的主承力構件仍主要使用金屬材料,這就不可避免地要對復合材料結構和金屬構件進行連接.由于復合材料的各向異性和多模式損傷形式,其與金屬的連接部位成為整個結構的薄弱部位.飛行器的復合材料G金屬結 構 件 有 70% 以 上 的 破 壞 都 發(fā) 生 在 連 接 部位[1],因此,對復合材料和金屬的連接性能進行研究具有重要的工程意義.
累積損傷有限元分析方法被廣泛應用于復合材料結構的各種受載分析中.CHANG[2]、TAN[3G4]和SLEIGHT[5]等很早就應用累積損傷有限元分析方法對復合材料結構進行了損傷分析,分析結果與試驗數(shù)據較吻合.此后,許多研究者在利用該方法對復合材料結構進行損傷分析和強度預測等方面均取得了很好的結果[6G10].累積損傷有限元分析方法主要包括應力分析、失效判定和材料性能退化準則[11G13],其主要采用的失效判定準則有最大應力準則[14]、Hashin準則[15]、Chang準則[16]和 Puck 準則[17]等.這些準則大多以應力作為參考值,這是因為在有限元算法中,單元損傷前后的應力變化比較劇烈,而應變變化比較平緩.目前,基于應變的失效判定準則研究較少,且在復合材料G金屬連接結構方面的應用更少.因此,作者以某型飛機機身尾段典型連接結構(復合材料G金屬連接結構)為研究對象,利用 ANSYS有限元軟件建立了該連接結構的三維有限元模型,應用累積損傷分析方法對該連接結構進行了失效預測及破壞規(guī)律研究,并進行了試驗驗證,為該型結構在工程上的應用提供參考
1 試驗方法與結果
1.1 試樣制備與試驗方法
試樣取自飛機尾端與后機身連接部位,尺寸如圖1所示.
試樣由一塊 LY12鋁合金板和一塊復合材料層合板通過兩排鈦合金抗剪型100°沉頭高鎖螺栓 YSA302G5G7A 和 高 鎖 螺 母 YAS361G5 連 接.復合材料層合板由3238A 環(huán)氧樹脂/CF3031碳纖維織物(簡稱3238A/CF3031)預浸料和3238A 環(huán)氧樹脂/CCF300碳 纖 維 (簡 稱 3238A/CCF300)預 浸料按一定方式鋪層后,在300 ℃固化3h 而得到.3238A/CF3031、3238A/CCF300預浸料的單層厚度分別為0.23,0.125mm,鋪層方案為(±45)/(0/90)/0/(±45)2/0/(0/90)/(±45)/0/(±45)/0/(±45)/0/(±45)/0/(±45)/(0/90)/0/(±45)2/0/(0/90)/(±45).制備得到的復合材料層合板厚4.45 mm.LY12鋁合金板的厚度為3mm,熱處理狀態(tài)為 T3.
按圖1所示位置,在試樣上粘貼 SDY2206靜態(tài)電阻應變片,采用 MTS810型強度試驗機進行室溫靜載拉伸試驗.試樣上下兩端夾持,下端加載,加載速率為1kN??s-1,每次達到5kN的倍數(shù)時保載10s,隨后繼續(xù)加載.此外,在試樣上加裝了防彎夾具(如圖2所示)后,在相同條件下再進行了室溫靜載拉伸試驗.
1.2 試驗結果與討論
在靜載拉伸時發(fā)現(xiàn):當加載載荷達到67.4kN時,未加裝防彎夾具試樣發(fā)出脆響;當加載至75kN時,在連接螺栓處出現(xiàn)凸起;繼續(xù)加載,試樣發(fā)出連續(xù)的脆響,出現(xiàn)載荷降低現(xiàn)象,螺栓處凸起更加明顯;當加載至79.6kN 時,試樣從連接處脫開.加裝防彎夾具試樣在加載至69.2kN 時發(fā)出脆響,復合材料層合板的部分接頭處出現(xiàn)損傷,但載荷無降低現(xiàn)象;加載至80kN 時,試樣出現(xiàn)連續(xù)響聲;加載至84.8kN 時,聽到 巨 大 脆 響,試 樣 從 連 接 處 完 全 脫開,載荷迅速回落.由圖3(a)可以看出,未加裝防彎夾具的試樣在拉伸破壞后出現(xiàn)了明顯的彎曲現(xiàn)象.這是因為鋁合金和復合材料的厚度不同,拉伸時載荷在螺栓連接處產生了較大的彎矩,導致試樣發(fā)生彎曲.而在實際結構中,連接部位通常有桁條或壁板支持,抗彎能力較強,因此,為得到該結構的實際拉伸破壞載荷,試樣需要加裝防彎夾具.由圖3(b)可見:加裝防彎夾具拉伸后,試樣中的復合材料表現(xiàn)為局部的粉碎性破壞,從接頭螺栓安裝孔位置沿螺栓擠壓方向至復合材料板端部被完全破壞;破壞位置可見纖維斷裂和纖維拔出現(xiàn)象,而分層現(xiàn)象則主要出現(xiàn)在螺栓孔部位兩側的區(qū)域內.這說明在整個加載過程中,試樣基體局部以及連接界面發(fā)生了嚴重的破壞.無防彎夾具時,破壞模式為拉脫破壞,試樣發(fā)生明顯彎曲;加裝防彎夾具后,試樣發(fā)生擠壓破壞.?。梗?deg;方向的應變片,即圖1中應變片3,6,9,12,15,18的應變值作載荷G應變曲線.由圖4可以看出:在拉伸初始階段,試樣的應變隨載荷的增加呈線性變化,應變變化比較均勻;各測點的應變變化趨勢相同,鋁合金板上的應變(即應變片12,15,18測得的應變)高于復合材料上的(即應變片3,6,9測得的應變);當加載至70kN 左右時,應變隨載荷的增大呈非線性變化,推測是因為連接結構內部出現(xiàn)了局部損傷,損傷擴展對應變產生了影響.
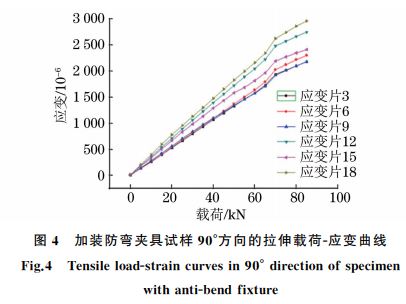
由表1可以看出,加裝防彎夾具后,試樣試驗數(shù)據的分散性很小,且破壞載荷相對無防彎夾具試樣的有所 增 大. 加 裝 防 彎 夾 具 后 的 試 驗 結 果 更 加準確.
2 有限元建模與分析
2.1 有限元模型
在 ANSYS有限元軟件中建模,采用8節(jié)點三維層狀體單元SOLID46模擬復合材料層合板,用8節(jié)點體單元SOLID45模擬鋁合金板與高鎖螺栓.為準確得到螺栓孔周邊的應力、應變分布,對網格進行局部細化.假設高鎖螺栓與復合材料層合板、鋁合金板接頭連接孔為無間隙配合,復合材料G金屬連接結構中的螺栓孔壁受高鎖螺栓擠壓發(fā)生變形,同時螺栓受到拉伸載荷和剪切載荷作用發(fā)生變形.為合理模擬高度非線性的接觸行為,采用 ANSYS軟件中面G面接觸單元 TARGET170和 CONTA174來定義接觸對.為模擬試驗中防彎夾具的效果,在模型外表面設置了垂直于表面方向的位移約束.復合材料G金屬連接結構三維有限元計算模型如圖5所示.
2.2 失效準則
由于有限元模型單元失效前后的應力變化劇烈,而應變變化相對平緩,因此為了正確判斷復合材料G金屬連接結構在拉伸過程中的主要損傷模式(基體破壞、纖維斷裂和分層失效),在其累積損傷模型中,采用 Hashin準則和 Ye分層準則[18]作為復合材料失效判據,根據應力G應變關系,將基于應力描述的失效準則轉換為基于應變描述的失效準則,進行失效預測分析.
假定復合材料單層的彈性常數(shù)不受層合板中相鄰層的影響,則單層材料主方向的應力G應變關系為
式中:σ為拉伸強度;τ為剪切強度;ε為拉伸應變;γ為剪切應變;下標1,2,3分別代表纖維軸向、纖維橫向和單層板法向;Cij 為剛度系數(shù).通過式(1)推 導 建 立 基 于 應 變 描 述 的 失 效 準則,纖維拉伸失效(ε1 >0)、纖維壓縮失效(ε1 <0)、基體拉伸或剪切失效(ε2 >0)、基體壓縮或剪切失效(ε2 <0)和分層失效準則分別為
式中:ε11,ε22和ε33 分別為1,2,3方向的應變,上標T 和 C分別表示拉伸和壓縮;γ012,γ013 和γ023 分別為對應于剪切強度τ12,τ13和τ23的剪切應變.
2.3 材料性能退化準則
在復合材料層合板承受外加載荷時,當其結構內部單元的應力、應變滿足式(2)~式(6)之一時,可認為這些單元失效,需要對失效單元的材料性能進行退化處理.對于損傷過程中的材料性能退化,研究人員提出了多種退化模型[19G21].作者對其中的Camanho損傷退化模型進行了改進,得到的材料性能退化準則的具體描述如下:
(1)纖維拉伸失效時,假設該失效單元不能承受任何載荷,E1,G12,G13,ν12,ν13 退化為初始值的1%,E2,E3,G23,ν23退化為初始值的6%(E 為彈性模量,G 為剪切模量,ν為泊松比).
(2)纖維壓縮失效時,假設該失效單元不能承受任何載荷,E1,G12,G13,ν12,ν13 退化為初始值的2%,E2,E3,G23,ν23退化為初始值的12%.
(3)基體拉伸或剪切失效時,E2,ν12 退化為初始值的1%,G12,G23,ν23退化為初始值的10%.
(4)基體壓縮或剪切失效時,E2,ν12 退化為初始值的2%,G12,G23,ν23退化為初始值的20%.
(5)分層失效時,E3,G13,G23,ν13,ν23退化為初始值的2%.實際上,損傷機理具有相互關聯(lián)性,一種類型的損傷可能誘發(fā)其他類型的損傷.對于包含多種損傷類型的局部損傷區(qū)域,應采用相應損傷類型的材料退化方式進行疊加.
2.4 累積損傷
由圖6可以看出:當靜拉伸載荷增至65kN 時,復合材料層合板與金屬連接處出現(xiàn)明顯損傷,即初始破壞載荷為65kN,損傷從復合材料層合板接頭螺栓安裝孔受擠壓區(qū)域產生;初始破壞載荷模擬值與靜拉伸試驗結果(68.3kN)相近,相對誤差僅為4.8%;隨著載荷的增大,復合材料層合板的損傷逐漸累積,并主要沿螺栓擠壓方向擴展;當載荷增至75kN 后,損傷迅速擴展,失效單元數(shù)量大大增加;當載荷達到90kN時,復合材料層合板的損傷區(qū)域擴展至其與金屬連接的端部,導致該復合材料G金屬結構連接件失去承載能力,即最終破壞載荷為90kN,模擬結果高于靜拉伸試驗測試結果(84.5kN),相對誤差為6.5%.對比圖6和圖3(b)可知,模擬得到的復合材料層合板損傷部位與試驗結果吻合較好.
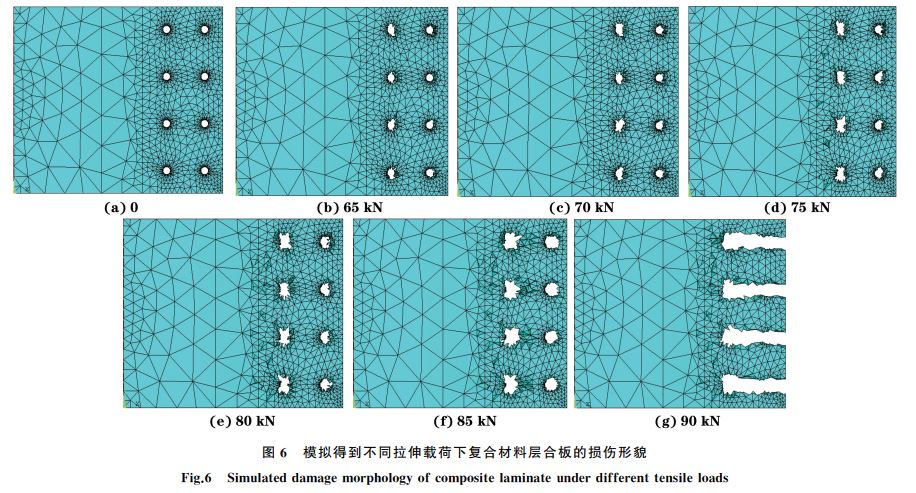
3 結 論
(1)復合材料G金屬連接結構件試樣在加裝防彎夾具后,其平均拉伸破壞載荷由未加裝防彎夾具
的79.6kN 增加到84.5kN,拉伸破壞模式由拉脫破壞變?yōu)閿D壓破壞.
(2)加裝防彎夾具后,復合材料G金屬連接結構件試樣在較小的拉伸載荷下,其應變隨載荷的增加呈線性增大,當拉伸載荷大于70kN 后,應變與載荷呈非線性變化;在金屬上的應變明顯大于復合材料層合板上的.
(3)模擬得到復合材料G金屬連接結構件的初始破壞載荷為65kN,與靜拉伸試驗得到的68.3kN接近,相對誤差為4.8%;最終破壞載荷為90kN,與拉伸試驗值的相對誤差為6.5%;損傷從復合材料層合板接頭螺栓安裝孔受擠壓區(qū)域產生,隨著載荷的增加而逐漸累積,并主要沿螺栓擠壓方向擴展,連接結構件出現(xiàn)擠壓破壞,與試驗結果相符.該復合
材料G金屬連接結構三維有限元累積損傷模型能夠有效預測復合材料G金屬連接結構件的損傷擴展過程及破壞模式.