分享:42CrMo鋼高強(qiáng)度螺栓軸向開(kāi)裂失效分析
滕 ?。?梁 博1,孫曉庭1,丁志敏2
(1.中車大連機(jī)車車輛有限公司,大連 116022;2.大連交通大學(xué),大連 116000)
摘 要:某8.8級(jí)42CrMo鋼高強(qiáng)度螺栓,在熱處理后滾絲過(guò)程中發(fā)生軸向開(kāi)裂.利用化學(xué)成分分析、宏觀檢驗(yàn)以及金相檢驗(yàn)等方法對(duì)螺栓開(kāi)裂原因進(jìn)行了分析.結(jié)果表明:螺栓開(kāi)裂主要是因?yàn)槠湓牧媳砻娲嬖诔示€狀分布的鍛造折疊缺陷,折疊缺陷末端形成應(yīng)力集中,在熱處理淬火時(shí)成為了裂紋源,于強(qiáng)大的淬火應(yīng)力和滾壓應(yīng)力作用下誘發(fā)了螺栓軸向開(kāi)裂.
關(guān)鍵詞:高強(qiáng)度螺栓;軸向開(kāi)裂;鍛造折疊缺陷;應(yīng)力集中;淬火開(kāi)裂
中圖分類號(hào):TG115.21 文獻(xiàn)標(biāo)志碼:B 文章編號(hào):1001G4012(2017)04G0296G03
FailureAnalysisonAxialCrackingofa42CrMoSteelHighStrengthBolt
TENG Wei1,LIANGBo1,SUNXiaoGting
1,DINGZhiGmin2
(1.CRRCDalianCo.,Ltd.,Dalian116022,China;2.DalianJiaotongUniversity,Dalian116000,China)
Abstract:A8.8gradehighstrengthboltmadefrom 42CrMosteelcrackedalongtheaxisduringthread
rollingprocessafterheattreatmentandthecrackingcausesofthebolt wereanalyzedby meansofchemical
compositionanalysis,macroexaminationandmetallographicexamination.Theresultsshowthatthecrackingofthe
boltwasmainlyduetothattherewaslineardistributionforgingfolddefectintheraw materialsurfacebeforeheat
treatment.Andtheforgingfolddefectcausedstressconcentrationandbecameacrackingsourcewhenquenching,
whichinducedtheaxialcrackingoftheboltundertheactionofpowerfulquenchingstressandrollingstress.
Keywords:highstrengthbolt;axialcracking;forgingfolddefect;stressconcentration;quenchingcracking
某 單 位 生 產(chǎn) 的 規(guī) 格 為 M16 mm×70 mm 的8.8級(jí)高強(qiáng)度螺栓為一種大批量生產(chǎn)的標(biāo)準(zhǔn)件.近日,在批量的滾絲生產(chǎn)過(guò)程中發(fā)現(xiàn)有個(gè)別螺栓發(fā)生軸向開(kāi)裂,如圖1所示.該螺栓材料為42CrMo鋼,生產(chǎn)工藝流程為:下料→墩頭→退火→調(diào)質(zhì)→精加工→滾絲.筆者對(duì)軸向開(kāi)裂螺栓進(jìn)行了檢驗(yàn)和分析,以期查明其開(kāi)裂原因,為采取有效預(yù)防措施、避免類似質(zhì)量問(wèn)題的再發(fā)生提供參考.
1 理化檢驗(yàn)
1.1 化學(xué)成分分析
對(duì)開(kāi)裂 螺 栓 取 樣 進(jìn) 行 化 學(xué) 成 分 分 析,結(jié) 果 見(jiàn)表1,可見(jiàn)各元素含量均符合 GB/T3077-2015«合金結(jié)構(gòu)鋼»對(duì)42CrMo鋼成分的技術(shù)要求.
1.2 宏觀檢驗(yàn)
將開(kāi)裂的螺栓沿縱向裂紋打開(kāi)后其宏觀形貌如圖2所示,可見(jiàn)斷口表面覆蓋黑色氧化皮,斷裂微觀形貌基本已無(wú)法辨別,但宏觀上依舊可判別裂紋的走向,裂紋從六角頭頂部及螺栓桿部表面呈一定弧度向基體擴(kuò)展,兩個(gè)方向擴(kuò)展的裂紋在六角頭內(nèi)部近表面區(qū)域發(fā)生交匯,如圖2中箭頭所指.
1.3 非金屬夾雜物檢驗(yàn)
從 開(kāi) 裂 的 螺 栓 上 截 取 縱 向 試 樣(取 樣 部 位 如圖1所示),經(jīng)鑲嵌、磨拋后進(jìn)行非金屬夾雜物檢驗(yàn).依據(jù) GB/T10561-2005«鋼中非金屬夾雜物含量的測(cè)定———標(biāo)準(zhǔn)評(píng)級(jí)圖顯微檢驗(yàn)法»,非金屬夾雜物含量檢驗(yàn)結(jié)果如下:A1.5,B0.5,C0.5,D0.
1.4 金相檢驗(yàn)
從開(kāi)裂螺栓裂紋部位切取橫向試樣,經(jīng)鑲嵌、磨拋后在光學(xué)顯微鏡下觀察,圖3為裂紋開(kāi)口處形貌,可見(jiàn)裂紋由表面向內(nèi)部擴(kuò)展,并呈現(xiàn)沿晶擴(kuò)展特征,裂紋內(nèi)部有氧化物.侵蝕后再觀察,裂紋兩側(cè)未見(jiàn)明顯的氧化脫碳現(xiàn)象,不具有鍛造折疊裂紋的特征,與淬火裂紋相似.
圖4為螺栓基體顯微組織形貌,為正常的回火索氏體,晶粒度依據(jù) GB/T6394-2002«金屬平均
晶粒度測(cè)定法»評(píng)定為7~8級(jí).在螺栓六角頭頂部取樣,經(jīng)鑲嵌、磨拋后在光學(xué)顯微鏡下觀察,圖5為六角頭頂部拋光態(tài)形貌,可見(jiàn)深約70μm 的二次裂紋,與金屬表面呈銳角,裂紋兩側(cè)存在高溫氧化質(zhì)點(diǎn)及內(nèi)氧化,侵蝕后進(jìn)行觀察,有氧化脫碳現(xiàn)象,具有鍛造折疊的特征[1].
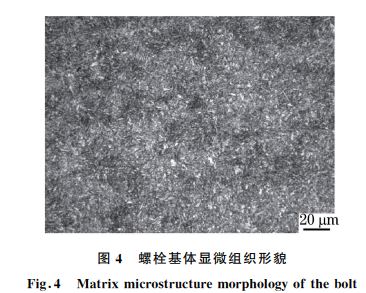
由于螺栓桿部及螺紋部位調(diào)質(zhì)處理后進(jìn)行了機(jī)加工,故其裂紋源信息已被破壞,無(wú)法進(jìn)行有效的判別,但根據(jù)螺栓斷口形貌及六角頭頂部的顯微形貌大致可以推測(cè),該螺栓在鍛造過(guò)程中六角頭頂部及桿部均存在較淺的折疊類缺陷,由于缺陷在調(diào)質(zhì)處理過(guò)程中未能去除,故而在淬火應(yīng)力下發(fā)生開(kāi)裂,裂紋分別由六角頭頂部和桿部同時(shí)萌生并向基體擴(kuò)展,由于存在兩個(gè)方向形成的裂紋,在裂紋擴(kuò)展過(guò)程中必然會(huì)存在交匯區(qū)域.螺栓的斷口形貌及金相形貌證實(shí)了這一觀點(diǎn).
分析與討論
從以上理化檢驗(yàn)結(jié)果可知,該螺栓的化學(xué)成分符合標(biāo)準(zhǔn)技術(shù)要術(shù),鋼中的非金屬夾雜物含量較低,這表明該螺栓材料的潔凈度較好;螺栓基體顯微組織為正常的回火索氏體,晶粒度為7~8級(jí),表明該螺栓調(diào)質(zhì)熱處理工藝正常.該螺栓的生產(chǎn)流程已經(jīng)定型,為 成 熟 工 藝. 同 批 次 熱 處 理 的 螺 栓 共 有7000個(gè)左右,僅發(fā)現(xiàn)6個(gè)螺栓發(fā)生了軸向開(kāi)裂,開(kāi)裂比例很低,屬于偶然失效,可以排除螺栓的淬裂是由于熱處理工藝和熱處理操作等因素造成的.裂紋通常起源于零件的應(yīng)力集中處,或在各種工藝過(guò)程中所造成的材料缺陷處[2].而材料缺陷形成應(yīng)力集中引起的裂紋一般起源于材料的折疊、拉痕、偏析等陷處[3G4].鍛造折疊和微裂紋同屬于應(yīng)力集中敏感區(qū)域,容易誘發(fā)熱處理開(kāi)裂.該螺栓表面裂紋為軸向擴(kuò)展,幾乎呈直線狀,開(kāi)裂起源于螺栓表面,裂紋邊上的小裂紋周圍存在脫碳現(xiàn)象,尾端圓鈍,具有鍛造折疊特征,折疊的末端為應(yīng)力集中點(diǎn),往往在熱處 理 淬 火 時(shí) 引 發(fā) 開(kāi) 裂[5G6].該 螺 栓 原 材 料 下 料 時(shí)為?17mm的棒材,在棒材拉拔過(guò)程中,原材料上的鍛造折疊缺陷沿軸向伸長(zhǎng)變形,在淬火應(yīng)力和折疊裂紋引起的應(yīng)力集中效應(yīng)的雙重作用下形成淬火裂紋,導(dǎo) 致 螺 栓 在 后 續(xù) 的 加 工 過(guò) 程 中 發(fā) 生 軸 向開(kāi)裂[7G8]。
結(jié)論
螺栓軸向開(kāi)裂與材料本身存在折疊缺陷有關(guān);該螺栓在熱處理前其表面即已存在呈線狀分布的鍛造折疊缺陷,折疊缺陷末端為應(yīng)力集中敏感區(qū)域,在淬火熱處理時(shí)成為了裂紋源,于強(qiáng)大的淬火應(yīng)力和滾壓應(yīng)力作用下誘發(fā)了軸向開(kāi)裂。
(材料測(cè)試網(wǎng)-理化檢驗(yàn)-物理分冊(cè))
“推薦閱讀”
【責(zé)任編輯】:國(guó)檢檢測(cè)版權(quán)所有:轉(zhuǎn)載請(qǐng)注明出處