分享:鋁化物涂層改性Super304H 鋼 在模擬鍋爐煤灰/氣環(huán)境中的腐蝕行為
鋁化物涂層改性Super304H 鋼
在模擬鍋爐煤灰/氣環(huán)境中的腐蝕行為
李 琰1,2,魯金濤1,楊 珍1,黃錦陽1,周永莉1,朱 明2
(1.西安熱工研究院有限公司,國家能源清潔高效火力發(fā)電技術(shù)研究中心,西安 710032;
2.西安科技大學(xué)材料科學(xué)與工程學(xué)院,西安 710054)
摘 要:利用粉末包埋法在Super304H 鋼表面制備了鋁化物涂層,在模擬鍋爐煤灰/氣環(huán)境中對涂層改性前后的Super304H 鋼和 HR3C鋼分別進行了650,750℃腐蝕試驗,對比分析了其腐蝕行為及腐蝕機制.結(jié)果表明:鋁化物涂層主要由FeAl和Fe3Al相組成;在650℃腐蝕500h后,涂層改性前Super304H 鋼表面氧化膜出現(xiàn)大面積剝落,而涂層改性后的鋼表面則形成了均勻致密的Al2O3 膜;在750 ℃腐蝕時,涂層改性前Super304H 鋼在腐蝕200h后其表面氧化層完全剝落,而涂層改性后的鋼經(jīng)500h腐蝕后,表面氧化膜剝落較改性前的輕,比650 ℃時的嚴重;鋁化物涂層
提高了Super304H 鋼的耐腐蝕性能,但高鉻含量的 HR3C鋼在650℃和750℃下均表現(xiàn)出更好的耐腐蝕性能.
關(guān)鍵詞:煤灰/氣環(huán)境;高溫腐蝕;鋁化物涂層;Super304H 鋼
中圖分類號:TG172 文獻標志碼:A 文章編號:1000G3738(2017)05G0089G06
CorrosionBehaviorofAluminideCoatingModifiedSuper304HSteel
inSimulatedBoilerCoalGAsh/GasEnvironments
LIYan1,2,LUJintao1,YANGZhen1,HUANGJinyang
1,ZHOUYongli1,ZHU Ming2
(1.NationalEnergyR & DCenterofCleanandHighGEfficiencyFossilGFiredPowerGenerationTechnology,
Xi′anThermalPowerResearchInstituteCo.,Ltd.,Xi′an710032,China;
2.CollegeofMaterialsScienceandEngineering,Xi′anUniversityofScienceandTechnology,Xi′an710054,China)
Abstract:Aluminidecoatingwaspreparedonsurfaceofsuper304Hsteelusingpackcementation method.
Thenthecorrosiontestsat650 ℃ and750 ℃ wereconductedontheSuper304H steelbeforeandaftercoating
modificationandonthe HR3CsteelinsimulatedboilercoalGash/gasenvironment,respectively.Thecorrosion
behaviorandcorrosionmechanism wereanalyzedandcompared.Theresultsshowthatthecoatingwascomposedof
FeAlandFe3Alphases.Aftercorrosionat650 ℃ for500h,theoxidationfilm onthesurfaceofunmodified
Super304Hsteelwasspalledwithalargearea,whileanuniformanddenseAl2O3filmwasformedonthesurfaceof
coatingmodifiedSuper304Hsteel.ThesurfaceoxidationfilmofunmodifiedSuper304Hsteelwasspalledcompletely
aftercorrosionat750 ℃for200h,however,thespallationofsurfaceoxidationfilmofcoatingmodifiedsteelafter
corrosionat750℃for500hwasslighterthanthatofunmodifiedsteelwhilemoreseriousthanthatat650℃.The
aluminidecoatingimprovedthecorrosionresistanceofSuper304Hsteelsignificantly.ButtheHR3Csteelwithhigh
Crcontenthadarelativelygoodcorrosionresistanceat650 ℃ and750 ℃.
Keywords:coalGash/gasenvironment;hightemperaturecorrosion;aluminidecoating;Super304Hsteel
0 引 言
隨著超(超)臨界發(fā)電技術(shù)的發(fā)展,鍋爐的蒸汽溫度和 壓 力 不 斷 提 高 (再 熱 器 出 口 蒸 汽 溫 度 高 達620 ℃,其壁溫達到了670 ℃),這使得鍋爐煙氣側(cè)材料的腐蝕問題日益突出,給機組的安全運行帶來了極大的挑戰(zhàn).
目前,細晶強化的Super304H 鋼仍是機組末級過/再熱器的首選材料[1].據(jù)測算,管外壁溫度達到640~680 ℃,才能使蒸汽參數(shù)達到620 ℃級超(超)臨界二次機組的要求.因此,需要對 Super304H 鋼在更高溫度下的耐煙氣腐蝕性能進行進一步的研究.目前,針對Super304H 鋼在高溫?zé)煔鈧?cè)腐蝕行為的研究報道較多[2G4].已有結(jié)果表明,Super304H鋼的腐蝕過程受服役溫度、煙氣成分及煤灰組成等諸多因素影響,其中溫度和煙氣中的硫是最主要的影響因素[5].PETTERSSO 等[6]對18G8型不銹鋼在不同溫度下的腐蝕行為進行了研究,發(fā)現(xiàn)該不銹鋼的腐蝕速率隨溫度的升高明顯加快.NATESAN等[7]的研究亦證實了這一點,并指出腐蝕速率峰值出現(xiàn)在725 ℃左右,這與620 ℃二次再熱機組煙氣側(cè)的溫度相近,顯然,在此溫度下 Super304H 鋼會發(fā) 生 嚴 重 腐 蝕.STEINGBRZOZOWSKA[8] 和ZENG[9]等通過改變服役環(huán)境中的硫含量后發(fā)現(xiàn),隨著煙氣中硫含量的增加,合金的腐蝕進程顯著加快.實際鍋爐運行時的測試結(jié)果與之相符,燃燒低品質(zhì)煤(高硫、高鈉煤)會顯著加快鍋爐材料的腐蝕,導(dǎo)致早期失效[10].一些模擬煤灰/氣環(huán)境中的腐蝕
研究結(jié)果表明,煤灰黏附在金屬表面時會形成低熔點堿金屬硫酸鹽,在650 ℃及更高溫度下這些堿金屬鹽呈熔融態(tài),這加速了金屬腐蝕[9].由此可見,在更高的服役溫度及高硫煙氣下,Super304H 鋼的耐腐蝕性能較差,這限制了其進一步的應(yīng)用.為滿足更高等級超(超)臨界機組運行要求,所用材料問題的解決思路主要有兩種:一是用高強度和高耐蝕性的高溫合金來替代現(xiàn)役奧氏體耐熱鋼,如Inconel740H 合金等[11G12];二是對現(xiàn)役管材涂敷高溫防護涂層.由于前者成本過高且缺少服役運行數(shù)據(jù)支持,其應(yīng)用受到了限制;后者則因具有成本低、易實施等特點得到了廣泛應(yīng)用.研究發(fā)現(xiàn),涂敷
鋁化物涂層的 NiGCrGW 高溫合金具有良好的抗高溫氧化性能[13],但其耐熱腐蝕性能不佳[14G15],涂層與基體之間的元素擴散導(dǎo)致涂層退化嚴重.而鋁硅、鋁鉻涂層可以很好地解決上述鋁化物涂層的不足.王心 悅 等[16]研 究 發(fā) 現(xiàn),經(jīng) 鋁 硅 共 滲 處 理 后,M951合金表面形成連續(xù)的θGAl2O3 膜,合金耐腐蝕性能得到了顯著提高.而鋁鉻共滲涂層中因同時含有鋁元素和鉻元素,能大幅度提高 Super304H 鋼的抗高溫氧化和耐熱腐蝕性能[17].在已有研究基礎(chǔ)上,作者采用粉末包埋工藝在Super304H 鋼表面制備了鋁化物涂層,研究了涂層改性前后Super304H 鋼在模擬鍋爐煤灰/氣環(huán)境中的腐蝕行為,同時以高鉻含量(質(zhì)量分數(shù)為25%)的HR3C鋼為參比對象,從耐蝕元素含量的角度探討了降低合金腐蝕速率的控制措施,為現(xiàn)役及下一代鍋爐機組用材料的選擇提供參考.
1 試樣制備與試驗方法
試 驗 材 料 有Super304H鋼 ,名 義 化 學(xué) 成 分 如表1所示;FeAl粉和 NH4Cl粉,粒徑均為48mm,國藥集團提供;以 HR3C鋼作為耐腐蝕性能分析的參比對象,其名義化學(xué)成分見表1,該鋼中鉻元素含量較高,為高鉻鋼.
將Super304H 鋼 加 工 成 尺 寸 為15mm×10mm×2mm 的試樣,用1200# 砂紙打磨后,用酒精清洗、吹干.采用粉末包埋法在試樣表面制備鋁化物涂層.按照FeAl粉和 NH4Cl粉質(zhì)量比為98∶2配制混合粉,將試樣包埋在混合粉中,升溫至950 ℃保溫2h,隨爐冷卻,酒精清洗、吹干后待用.在模擬鍋爐煤灰/氣環(huán)境中進行腐蝕試驗.將含2% (質(zhì) 量 分 數(shù),下 同)Na2SO4,2%K2SO4,6%Fe2O3,22%Al2O3 和29%CaSO4 的合成煤灰刷涂于涂層改性前后 Super304H 鋼和 HR3C 鋼試樣表面,煤灰用量為40~50mg??cm-2,然后將試樣用合金絲串起 懸 掛 于 管 式 爐 中 進 行 腐 蝕,試 驗 裝 置 如圖1所示.管式爐中通入由1.5%(體積分數(shù),下同)SO2,3.5%O2,5%H2O,10%CO2 和 80%N2 混合組成的模擬煤氣,流量為100mL??min-1,催化劑為鉑網(wǎng),腐蝕試驗溫度分別為650,750 ℃.反應(yīng)后的尾氣用飽和氫氧化鈉溶液吸收后排出.在試驗過程中,每隔一段時間取出試樣并清洗干凈,稱取質(zhì)量,觀察后重新涂覆煤灰繼續(xù)試驗.
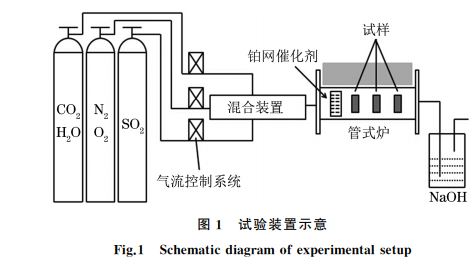
用精度為0.01mg電子天平稱取試樣質(zhì)量,計算腐 蝕 質(zhì) 量 變 化;用 HitachiGS4800 型 掃 描 電 鏡(SEM)觀察鋁化物涂層、腐蝕層表面和截面形貌,
并用 附 帶 的 能 譜 儀 (EDS)分 析 其 元 素 組 成;利 用ShimazduG7000SX 型 X 射線衍射儀(XRD)分析腐蝕產(chǎn)物的物相組成.為便于觀察腐蝕層形貌,部分腐蝕試樣進行了噴金及化學(xué)鍍鎳處理.
2 試驗結(jié)果與討論
2.1 鋁化物涂層的顯微組織
由圖2可知:采用粉末包埋法制備的鋁化物涂層分內(nèi)外兩層,厚度分別為40,15μm;涂層主要由FeAl和 Fe3Al相組成.由 EDS點成分分析可知,外層 和 內(nèi) 層 中 鋁 元 素 的 平 均 質(zhì) 量 分 數(shù) 分 別 為33.15%和12.43%.
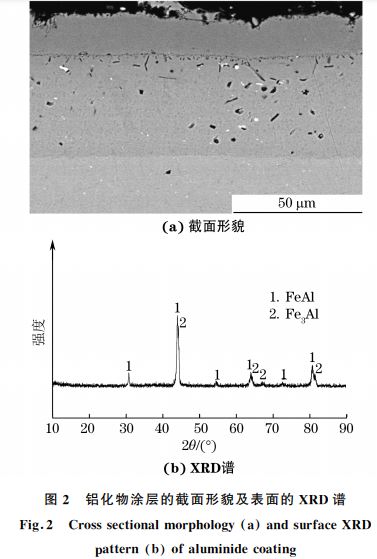
2.2 腐蝕質(zhì)量變化
由圖3可知:在650℃下,涂層改性前Super304H鋼在腐蝕初期的質(zhì)量增加較快,50h達到峰值,之后連續(xù)大幅下降,直至出現(xiàn)嚴重的腐蝕質(zhì)量損失;涂層改性 后 Super304H 鋼 的 腐 蝕 質(zhì) 量 增 加 緩 慢,在50h后 出 現(xiàn) 輕 微 的 下 降,腐 蝕 質(zhì) 量 損 失 較 小.在750℃下,涂層改性前Super304H 鋼在腐蝕20h后 出 現(xiàn) 嚴 重 的 腐 蝕 質(zhì) 量 損 失;涂 層 改 性 后Super304H 鋼在腐蝕前100h內(nèi)出現(xiàn)明顯的腐蝕質(zhì)量增加,200h后質(zhì)量增加緩慢下降.而 HR3C 鋼在兩種溫度下均表現(xiàn)出良好的耐腐蝕性能,腐蝕質(zhì)量增加變化較小.
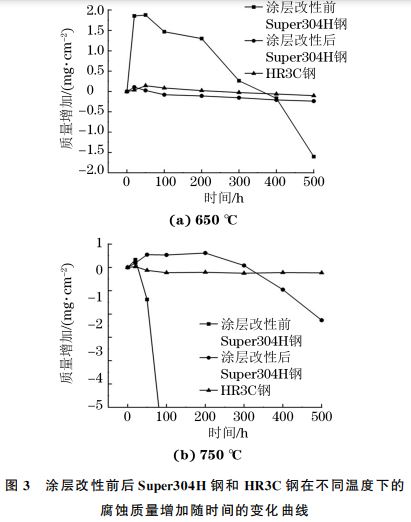
2.3 腐蝕產(chǎn)物形貌
由圖4可知:在650 ℃腐蝕500h后,涂層改性前 Super304H 鋼 發(fā) 生 了 明 顯 的 腐 蝕,表 面 氧 化膜大面積 剝 落,且 出 現(xiàn) 明 顯 的 分 層、斷 層 現(xiàn) 象,腐蝕層較 厚 (約 為 40μm);涂 層 改 性 后 Super304H鋼表面氧化膜相對平整,厚度均勻,未發(fā)生明顯的腐蝕剝落,腐蝕層中出現(xiàn)細小的針狀腐蝕產(chǎn)物,涂層與基體界面清晰可見;HR3C鋼表面形成了一層
致密、完整、很薄(厚度約為4μm)的氧化膜,氧化物顆粒細小.
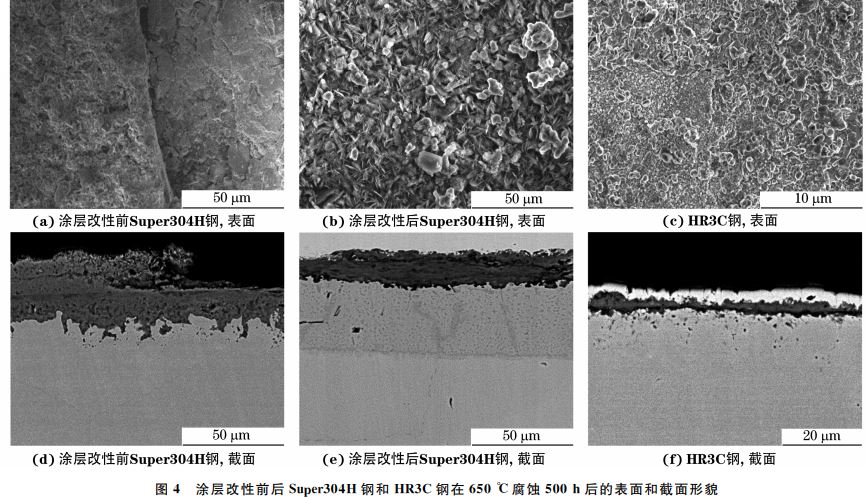
由圖5可知:在750 ℃腐蝕200h后,涂層改性前Super304H 鋼的表面氧化膜已完全脫落,基體內(nèi)部發(fā)現(xiàn)大量腐蝕產(chǎn)物;涂層改性后Super304H 鋼在腐蝕500h后表面氧化膜的剝落相對較少,但局部區(qū)域出現(xiàn)溶解腐蝕現(xiàn)象,與650 ℃腐蝕500h的相比,其表面針狀腐蝕產(chǎn)物的尺寸增大;鋁化物涂層與基體的界面均模糊不清,說明該涂層的耐腐蝕作用已逐漸減弱甚至消失.HR3C鋼表面氧化膜出現(xiàn)腐蝕破裂現(xiàn)象,氧化膜變得疏松多孔,與650 ℃腐蝕500h的相比,其氧化膜厚度明顯增大(約為12μm).
2.4 腐蝕產(chǎn)物組成
由圖6 可 知:在 650 ℃ 腐 蝕 后,涂 層 改 性 前Super304H 鋼表面腐蝕產(chǎn)物主要為 Fe2O3 和少量FeCr2O4;涂層改性后 Super304H 鋼表面腐蝕產(chǎn)物以 Al2O3 為 主. 在 750 ℃ 腐 蝕 后,涂 層 改 性 前Super304H 鋼表面除了上述腐蝕產(chǎn)物外,還出現(xiàn)少量硫化物;涂層改性后Super304H 鋼表面則生成了Fe2O3、Al2O3 和 FeAl2O4 等多種腐蝕產(chǎn)物.在兩種溫度下,HR3C 鋼表面的腐蝕產(chǎn)物基本不變,以Fe2O3 和 Cr2O3 為主,并存在少量 FeCr2O4.
2.5 分析與討論
在模擬煤灰/氣腐蝕環(huán)境中,鋼腐蝕是由低熔點堿金屬 硫 酸 鹽 及 氧 化/硫 化 交 互 加 速 作 用 而 導(dǎo) 致的[18G20],主要化學(xué)反應(yīng)如下:
2SO2+O2 ??????2SO3 (1)
3K2SO4+Fe2O3+3SO3 →2K3Fe(SO4)3 (2)
3Na2SO4+Fe2O3+3SO3 →2Na3Fe(SO4)3 (3)
Na3Fe(SO4)3 和 K3Fe(SO4)3 的熔點較低,分別為624 ℃和618 ℃.在試驗溫度下,這兩種鹽為熔融態(tài),可與涂層改性前Super304H 鋼表面的由氧和鉻、鐵所形成的氧化膜發(fā)生溶解反應(yīng).此時,環(huán)境中的硫、SO2/SO3 等腐蝕性介質(zhì)通過膜中的缺陷向膜內(nèi)擴散并與鋼中的合金元素生成網(wǎng)狀結(jié)構(gòu)的硫化物(FeS、CrS等),這為元素外擴散及腐蝕介質(zhì)的內(nèi)擴散提供了快速通道,加快了該鋼的腐蝕進程.隨著氧的內(nèi)擴散,部分內(nèi)硫化物被氧化釋放出活性硫,硫會繼續(xù)向內(nèi)擴散形成新的硫化物.此過程循環(huán)進行,因此在腐蝕層/基體界面處始終有硫化物的存在.通常情況下,硫化物陽離子空位濃度大,原子在硫化物 中 具 有 更 高 的 擴 散 速 率,且 其 分 子 體 積(PVB)較大,會增大膜層的內(nèi)應(yīng)力,導(dǎo)致氧化膜開裂或剝落[21].涂層改性前 Super304H 鋼的表面膜層以鐵的氧化物為主.由于 Fe2O3 的穩(wěn)定性較差,易發(fā)生硫酸鹽化,因此隨著腐蝕的進行,Fe2O3 膜逐漸被溶解失去保護性,導(dǎo)致該鋼腐蝕較嚴重.與650℃相比,涂層改性前Super304H 鋼在750 ℃腐蝕20h后出現(xiàn)嚴重的腐蝕質(zhì)量損失,至200h,表面氧化層已完全脫落,表現(xiàn)出極差的耐腐蝕性能,顯然,溫度的升高加快了膜層的溶解腐蝕進程.涂層改性后 Super304H 鋼的表面形成了連續(xù)致密、黏附性較強且穩(wěn)定的 Al2O3 保護膜.該膜層阻礙了腐蝕性氣體和熔鹽向鋼基體內(nèi)的擴散[22],且由于 Al2O3 膜具有一定的自修復(fù) 能 力,一 旦 被 破壞,鋁元素向表面遷移又會形成新的 Al2O3 膜,因此鋁化物涂層改性后Super304H 鋼的耐煤灰/氣腐蝕性能得到了大幅度提高.雖然涂層改性后 Super304H 鋼的耐腐蝕性能得到了顯著提升,但與高鉻含量的 HR3C 鋼相比其耐蝕性能仍舊較差.這主要有幾個方面的原因:一是涂層與基體中元素的互擴散會造成涂層中的鋁元素損失嚴重,導(dǎo)致該涂層失效[23G24];二是 Al2O3 膜層在熔鹽中的穩(wěn)定性較差,易發(fā)生硫酸鹽化出現(xiàn)溶解現(xiàn)象而導(dǎo)致涂層失效[25];三是由于向外擴散的鐵元素一方面被氧化形成 Fe2O3,另一方面與鋁反應(yīng)形成新的 Fe3Al層,隨著腐蝕時間的延長,Fe2O3 和FeAl2O4 逐漸增多,貫穿整個涂層,形成快速擴散通道,使涂層失去了對基體元素的阻擋作用,導(dǎo)致了涂層失效[14G15].從試驗結(jié)果看,Super304H 和 HR3C鋼雖同為奧氏體耐熱鋼,但在高溫煤灰/氣中的耐腐蝕性能差異較大.在試驗周期內(nèi),HR3C 鋼表現(xiàn)出了較佳 的 耐 腐 蝕 性 能,這 與 其 高 鉻 含 量 有 關(guān)[5].
Cr2O3 的形核和生長較快,通過選擇性氧化在較短時間內(nèi)就能在 HR3C 鋼表面形成一層連續(xù)致密的Cr2O3 保護膜.Cr2O3 膜在熔鹽中穩(wěn)定性較好,不易發(fā)生溶解腐蝕,大幅提高了 HR3C 鋼的耐腐蝕性能[26].綜上可見,鋁 化 物 涂 層 改 性 雖 可 顯 著 提 高Super304H 不銹鋼在煤灰/氣中的耐腐蝕性能,但HR3C鋼由于具有較高質(zhì)量分數(shù)的鉻使得其耐腐蝕性更加優(yōu)異.
3 結(jié) 論
(1)采用粉末包埋法在 Super304H 鋼表面制備了鋁化物涂層,該涂層分內(nèi)外兩層,厚度分別為40,15μm,該涂層主要由 FeAl和 Fe3Al相組成.
(2)在650 ℃模擬煤灰/氣中腐蝕后,鋁化物涂層改性前 Super304H 鋼的腐蝕質(zhì)量增加隨腐蝕時間的延長先增大,當腐蝕時間達到50h后大幅度下降,腐蝕500h后表面氧化膜大面積剝落,表面腐蝕產(chǎn)物主 要 為 Fe2O3 和 少 量 FeCr2O4;涂 層 改 性 后Super304H 鋼的腐蝕質(zhì)量增加明顯比涂層改性前的低,且變化較平緩,這主要是因為該鋼表面形成了
均勻致密的 Al2O3 膜,提高了其耐腐蝕性能.
(3)在750 ℃模擬煤灰/氣中腐蝕后,涂層改性前Super304H 鋼在腐蝕20h后出現(xiàn)嚴重的腐蝕質(zhì)量損失,腐蝕200h后其表面氧化膜完全剝落;涂層改性后Super304H 鋼經(jīng)500h腐蝕后,表面氧化膜剝落相對于涂層改性前鋼的少,但比650 ℃下腐蝕的嚴重,且表面針狀腐蝕產(chǎn)物尺寸增大,腐蝕產(chǎn)物主要為 Fe2O3、Al2O3 和 FeAl2O4 等.
(4)與鋁化物涂層改性 Super304H 鋼相比,高鉻含量的 HR3C 鋼在650 ℃和750 ℃下均表現(xiàn)出較好的耐腐蝕性能,鉻元素是提高此鋼耐腐蝕性能的關(guān)鍵.
晶界處富集銅元素的θ′(Al2Cu)相溶解,向 T1 相轉(zhuǎn)變,大量析出的強化相 T1 能有效阻礙位錯運動,從而形成彌散強化.接頭伸長率的下降與熱處理過程中接頭焊縫晶粒的長大、晶界析出相等導(dǎo)致位錯在晶界處塞積有關(guān).
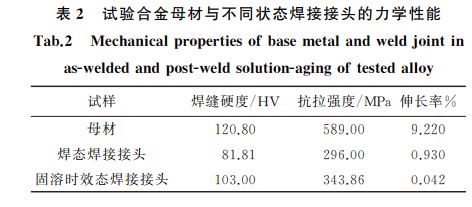
3 結(jié) 論
(1)在試驗條件下,2195GT8 鋁鋰合金激光焊接接頭獲得熔透且背部無明顯下塌焊縫的熱輸入Q約為160J??mm-1,在P=6kW,v=2.2m??min-1時試驗合金可以獲得成形良好,內(nèi)部無氣孔、裂紋等缺陷的焊接接頭.
(2)焊態(tài)下焊縫熔合線區(qū)的組織為細小的等軸晶,焊縫中心為等軸晶和粗大的樹枝晶;焊縫區(qū)的組織軟化嚴重,為整個焊接接頭的薄弱區(qū);與母材相比,焊縫的硬度下降了32.3%,焊接接頭的抗拉強度下降了約49%,斷裂形貌為沿晶脆性斷裂.
(3)經(jīng)過固溶時效處理后,合金焊縫的組織更加均勻,晶粒長大,同時晶界及晶內(nèi)析出許多彌散且較均勻分布的 T1(Al2CuLi)相,焊縫的硬度明顯升高,比固溶時效處理前的提高了25.6%,抗拉強度則提高了13.7%.